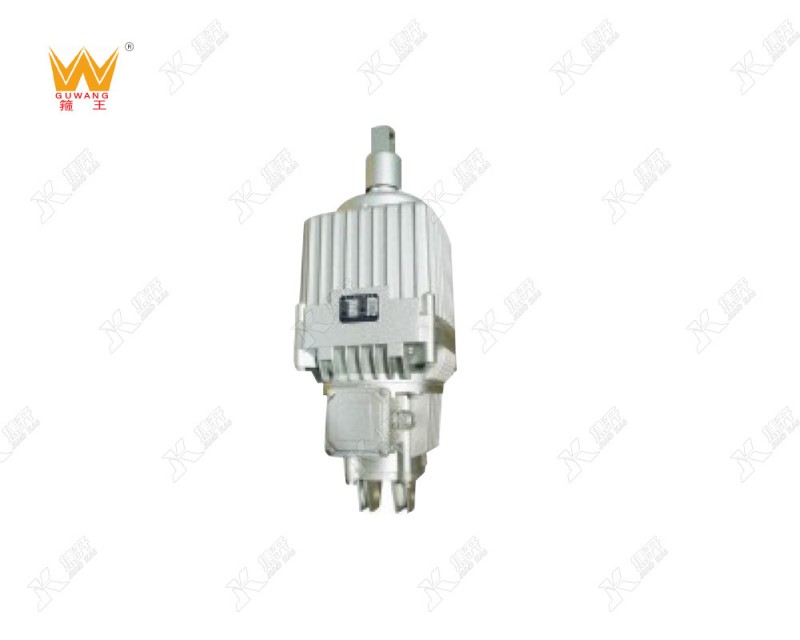
ED
Electric hydraulic thruster
Application:
Widely used in driving devices for various drum brakes and disc brakes, as well as in industrial valves, gates, directional swinging and rotating (<90°) devices, and clamping device drive control.
Widely used in driving devices for various drum brakes and disc brakes, as well as in industrial valves, gates, directional swinging and rotating (<90°) devices, and clamping device drive control.
Manufactured according to the original EMG (West Germany) technology. Compliant with DIN15430 and JB/T10603-2006 standards.
Features an aluminum alloy housing, fully sealed single push-rod structure, with a beautiful appearance, lightweight, and safe, reliable performance.
The motor is of non-oil-immersed structure, with F-class insulation, excellent heat resistance, and long lifespan.
The motor's junction box has good sealing, using cable glands for wiring, with a high protection level.
Both the motor shaft and push rod have undergone special surface treatment, significantly extending the life of the sealing elements.
The transmission parts use a double-seal structure, providing excellent sealing and reliable performance.
One side of the cylinder housing is equipped with a balance air chamber, allowing installation within a 0-180° range; the linkage can rotate 360°. Additional functions can be realized by adding optional components to the actuator.
Upper limit switch: Indicates whether the actuator's push rod has risen to the specified position (whether the brake is open).
Lower limit switch: Indicates whether the actuator's push rod has returned to the specified position (whether the brake is closed).
Upper valve or lower valve: Can extend the upper or lower time steplessly, with the adjustable maximum value being 10-20 times the rated value. For actuators with valves, the rising and falling time will be extended when fully open. For short-stroke actuators, the time extends by approximately 1~2 seconds, and for long-stroke actuators, by 2~4 seconds.
Brake spring: Generates pulling force for short-stroke actuators, mainly replacing the brake spring on the brake frame to produce braking force. In the technical parameters table, the "brake spring force" refers to the spring force when the actuator is 1/3 of the way through the rising stroke (2/3 through the falling stroke).
Return spring: Functions similarly to the brake spring but with smaller force. Its main role is to reset the actuator piston and its external connection components. The return spring force can also be customized by the user, but it must not exceed the brake spring force.
Buffer spring: Installed in place of the linkage on the actuator piston rod of short-stroke actuators, without changing the actuator's stroke. Mainly used to regulate the braking process and cushion the non-periodic transient process of braking, ensuring smooth braking. (Note: Actuators with buffer springs cannot be equipped with limit switches and must be used in conjunction with brake springs.)
Heater: If the ambient temperature is below -20°C, a heater can be installed according to user requirements. Heater voltage: AC110V or AC220V; heater power is listed in the table below. The method of temperature control and adjustment can be selected by the user.
Ambient temperature: :-20℃~50℃.From -20°C to 50°C, use DB-25 hydraulic oil.
For temperatures below -20°C, use YH-10 aviation hydraulic oil (in this case, a heater is not required). If using DB-25 hydraulic oil, a heater must be installed.
Relative humidity: No more than 90%.
Altitude requirements: Complies with GB755-2008 standards for altitude at the installation location.
Working environment: The environment should be free from flammable, explosive, or corrosive gases. If such gases are present, explosion-proof or corrosion-resistant models should be used.Motor specifications: - Insulation class: F - Protection rating: IP65.
Cabling: The maximum cross-sectional area for cable wires can be up to 4x25mm2.
Power supply: - Three-phase AC, 50Hz, 380V. - (Other voltage and frequency configurations are available upon request).
Duty cycle: S1 and S3-60%.